Capabilities Overview
Advanced Hermetic Solutions offers precision brazing, hermetic sealing, high-vacuum assembly, sensor packaging, and cleanroom integration, supported by advanced materials expertise and rigorous testing capabilities.
Precision Hermetic Sealing Solutions
Delivering high-reliability assemblies for extreme environments.
Vacuum Brazing
Vacuum brazing is a highly precise, flux-free joining process ideal for producing hermetically sealed and high-reliability assemblies. Our state-of-the-art vacuum furnaces operate at pressures below 10⁻⁵ Torr, ensuring exceptional cleanliness and oxidation-free joints essential for mission-critical applications.
- High-vacuum environment eliminates contamination and oxidation, producing ultra-clean brazed joints.
- Specializes in joining a wide range of dissimilar materials, including ceramics (Alumina, Sapphire), Kovar, Inconel, Stainless Steels (316L, 17-4PH), Titanium alloys, and refractory metals.
- Advanced fixturing and thermal cycle control to manage differential thermal expansion and material compatibility.
- Braze alloy options include gold-based, silver-copper eutectics, nickel-based, and palladium-enhanced systems for optimized mechanical, thermal, and corrosion performance.
- Precision leak testing available post-braze, ensuring hermeticity to 10⁻¹⁰ atm-cc/sec with helium mass spectrometry.
- Extensive process validation protocols to meet aerospace, semiconductor, defense, and medical device industry requirements.
Whether developing prototypes or supporting full production, our vacuum brazing services deliver repeatable, high-integrity joints critical for assemblies exposed to extreme environments and demanding operational cycles.
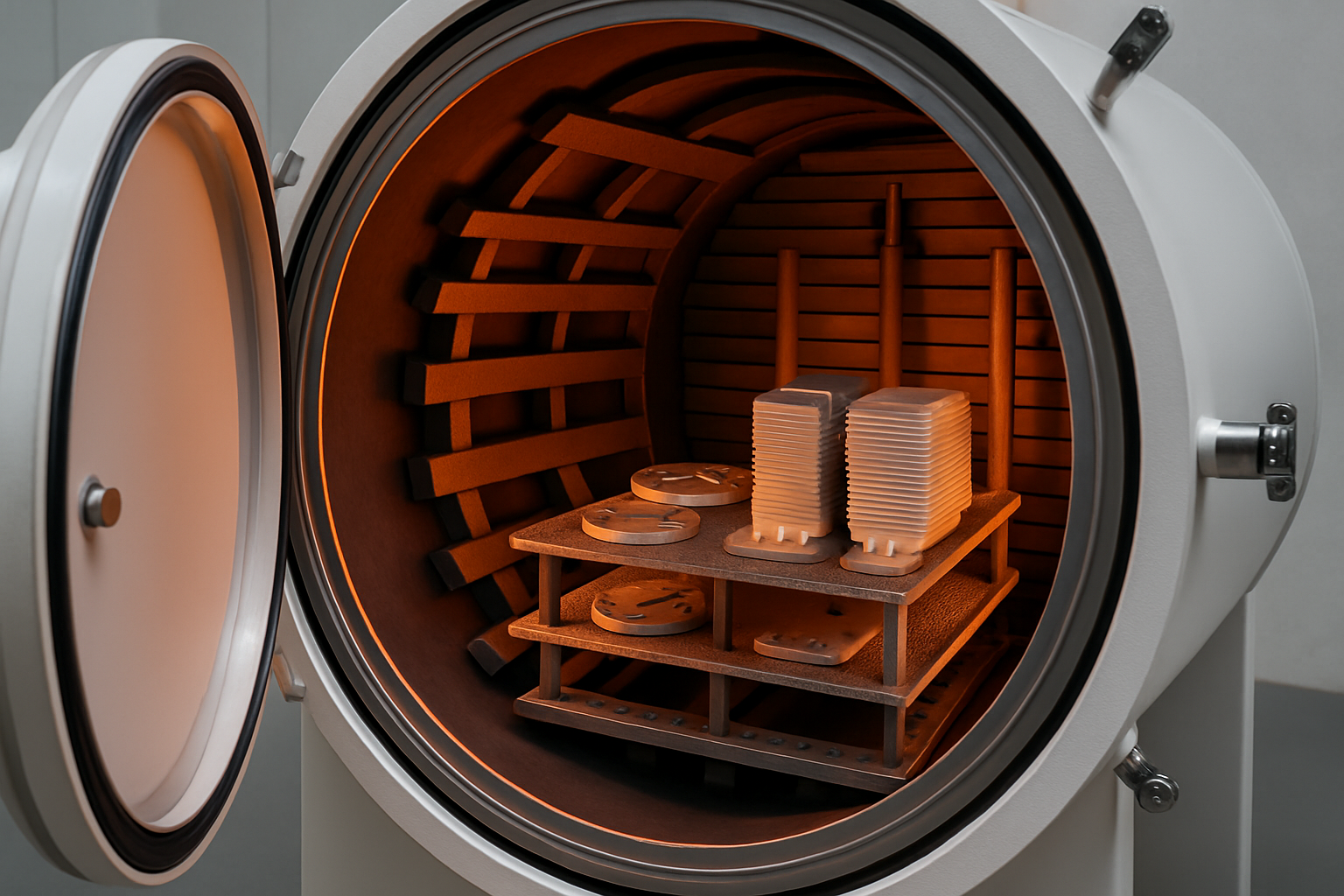
Hermetic Feedthroughs & Sensor Assemblies
Our hermetic feedthroughs and sensor assemblies are engineered to deliver reliable performance in extreme environments. We offer custom designs for electrical, optical, and hybrid feedthroughs, ensuring robust connections that maintain hermetic integrity under demanding operational conditions.
- Custom-engineered feedthroughs for electrical, fiber-optic, RF, and hybrid signal transmission.
- Helium leak rates certified to < 1x10⁻⁹ atm-cc/sec using high-sensitivity mass spectrometry.
- Designed for extreme environments including high-pressure, high-vibration, cryogenic, and elevated temperature applications.
- Material options include Kovar, titanium, Inconel, stainless steels, ceramics (alumina), and sapphire insulators.
- Gold and silver-based braze joints for superior corrosion and fatigue resistance.
- Solutions for aerospace, defense, semiconductor, oil & gas, and medical implantable applications.
- High-density multi-pin configurations and miniaturized assemblies available upon request.
Whether for satellites, implantable sensors, or deep-sea systems, our precision hermetic assemblies deliver trusted, leak-tight performance where failure is not an option.
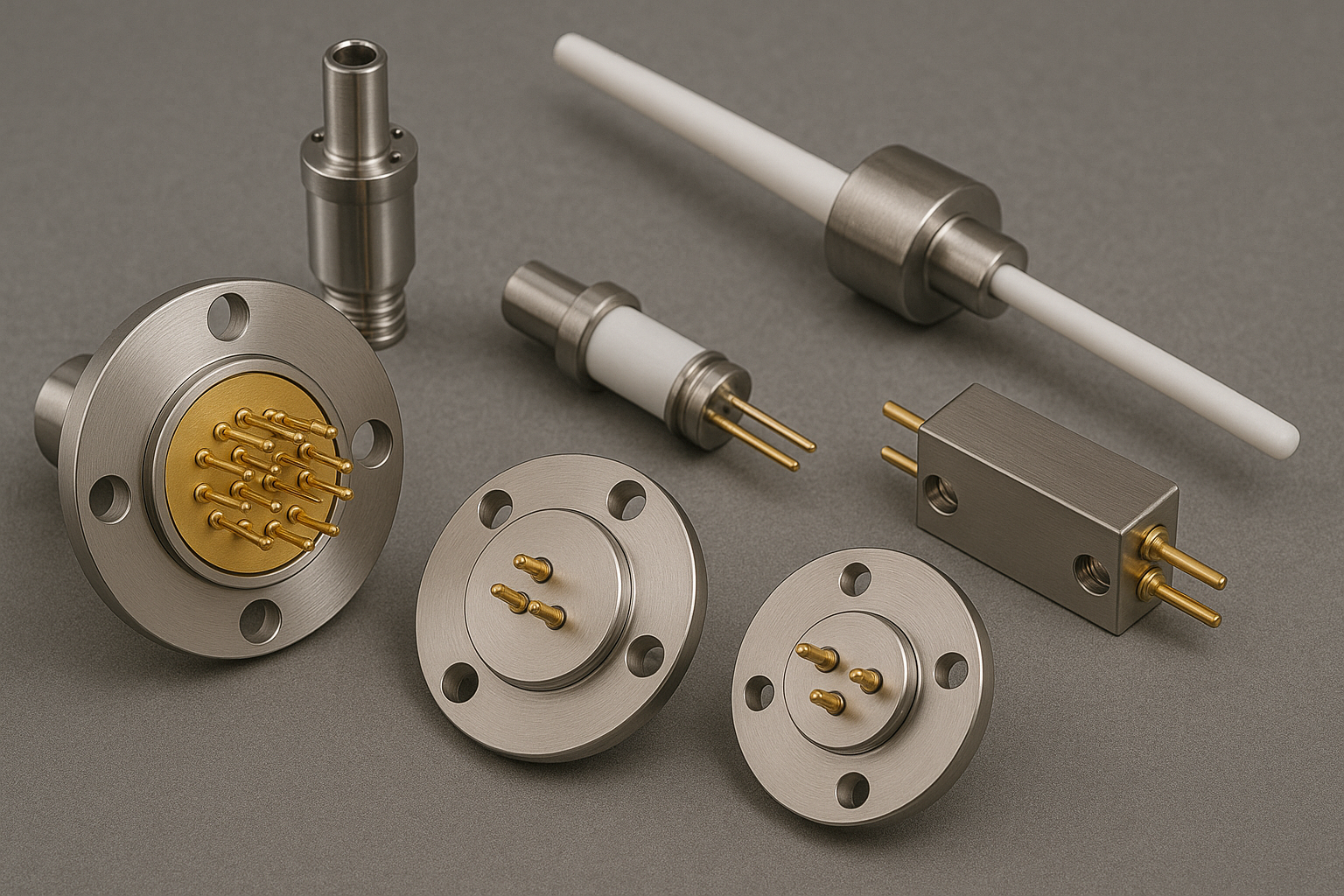
Sapphire-to-Metal Window Integration
We specialize in the precision brazing and sealing of sapphire, ruby, and quartz windows to metal housings for mission-critical optical and sensor systems. Our sapphire-to-metal integration technology ensures maximum optical clarity, mechanical strength, and leak-tight performance across extreme environments.
- Optical-grade active brazing of sapphire, ruby, quartz, and other crystalline materials to metals including titanium, Kovar, stainless steels, and Inconel.
- Custom window frames designed for lasers, optical sensors, imaging systems, and analytical instruments.
- Capable of withstanding high-pressure environments up to 30,000 psi and severe thermal cycling conditions.
- Low-distortion sealing techniques to preserve optical flatness, minimizing birefringence and optical scatter.
- Multi-layer metallization and braze systems optimized for adhesion, thermal expansion management, and hermeticity.
- Applications include aerospace sensor ports, medical diagnostic equipment, energy exploration tools, and semiconductor metrology windows.
- Surface finishes and anti-reflection coatings available upon request to enhance transmission and reduce reflectivity.
Our sapphire window assemblies combine mechanical resilience with superior optical performance, delivering unmatched durability and precision in the most demanding operational environments.
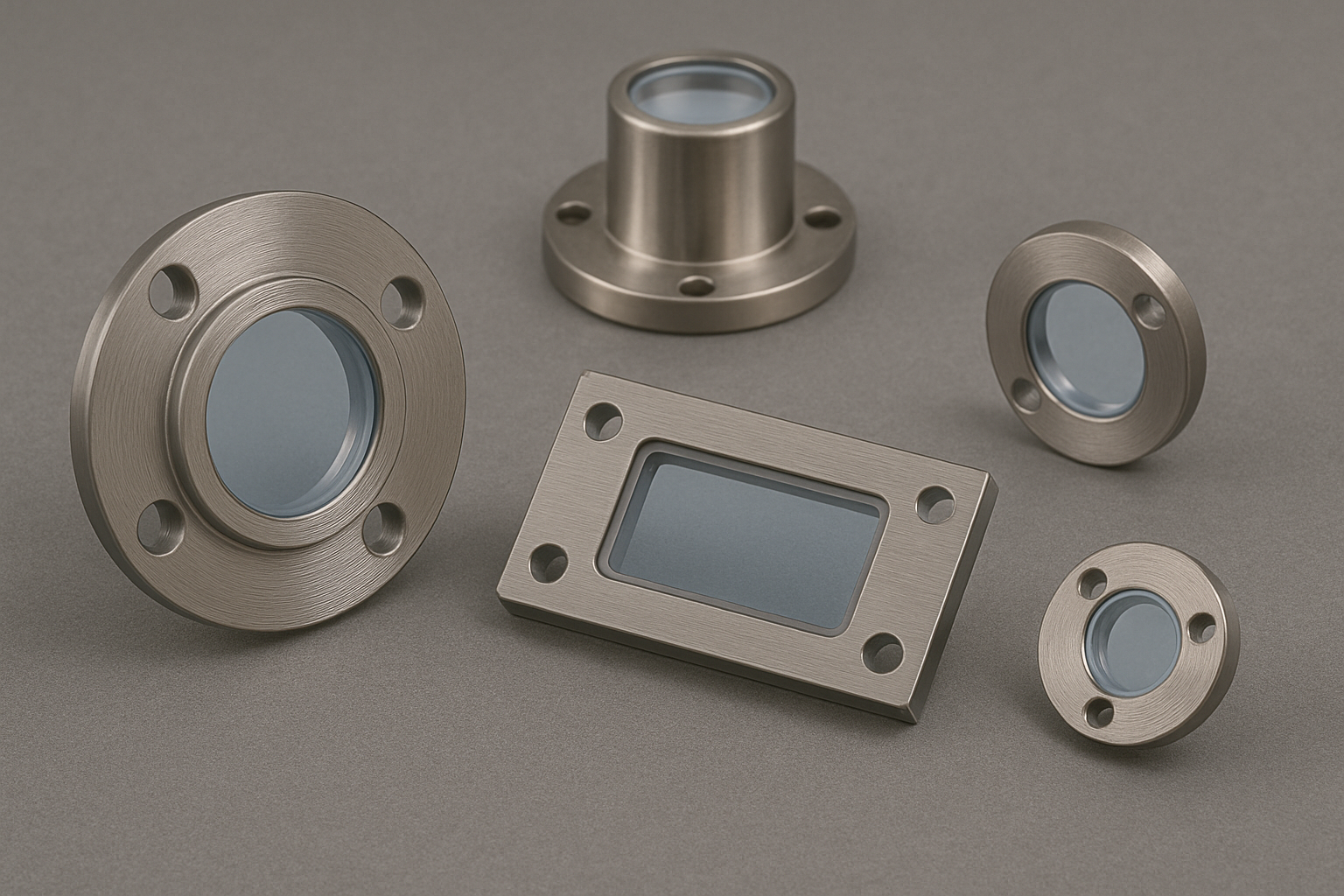
High-Pressure & Harsh-Environment Packaging
We engineer advanced packaging solutions capable of surviving the most extreme environments. Through metal-to-ceramic and glass-to-metal sealing technologies, we ensure robust protection for critical components exposed to high pressures, chemical exposure, radiation, and thermal cycling.
- Metal-to-ceramic and glass-to-metal transitions designed for high-reliability sealing under extreme conditions.
- Qualified for subsea, downhole, aerospace, and nuclear applications.
- Encapsulation techniques available for moisture barrier, chemical shielding, and mechanical reinforcement.
- Optional conformal coatings including parylene, ceramic, and polymeric films to enhance corrosion and dielectric protection.
- Specialized designs to accommodate high differential pressures and aggressive environments up to 30,000 psi.
Our solutions extend component life and reliability in oil and gas exploration, deep-sea communications, radiation detection, and high-vibration aerospace systems.
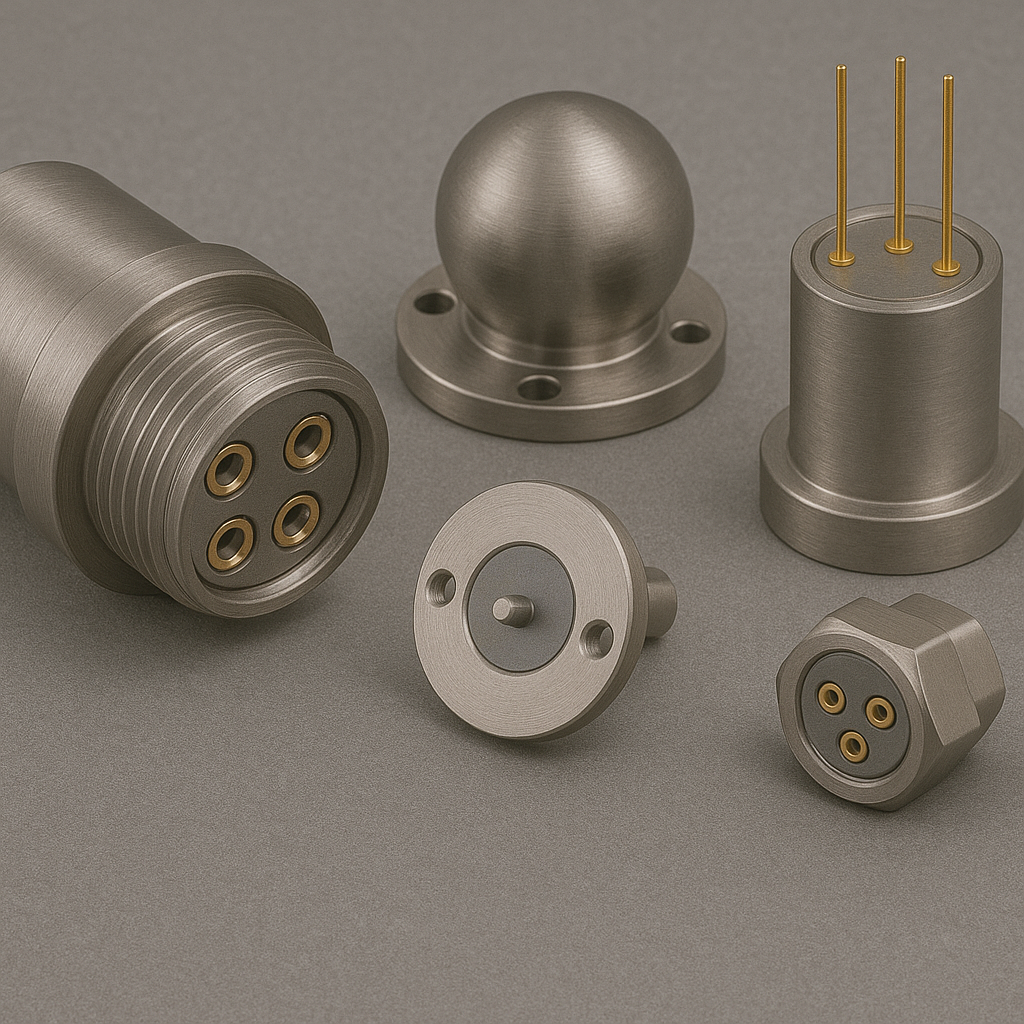
Cleanroom Assembly & Packaging
We offer precision cleanroom assembly and packaging services to meet the stringent requirements of aerospace, semiconductor, and medical device industries. Our ISO 7 (Class 10,000) certified cleanroom ensures particulate control, bioburden reduction, and contamination-free manufacturing.
- ISO 7 (Class 10,000) cleanroom certified for precision assembly of sensitive components.
- Ultrasonic cleaning and solvent processing of metal, ceramic, and glass parts to achieve high-purity surfaces.
- Final packaging options include vacuum sealing, nitrogen purging, double-bagging, and ESD-safe packaging.
- Controlled environmental monitoring and batch tracking for aerospace and medical device traceability standards.
- Custom kitting, labeling, and inventory management services available upon request.
Our cleanroom solutions protect product integrity from production through delivery, ensuring readiness for high-reliability applications.
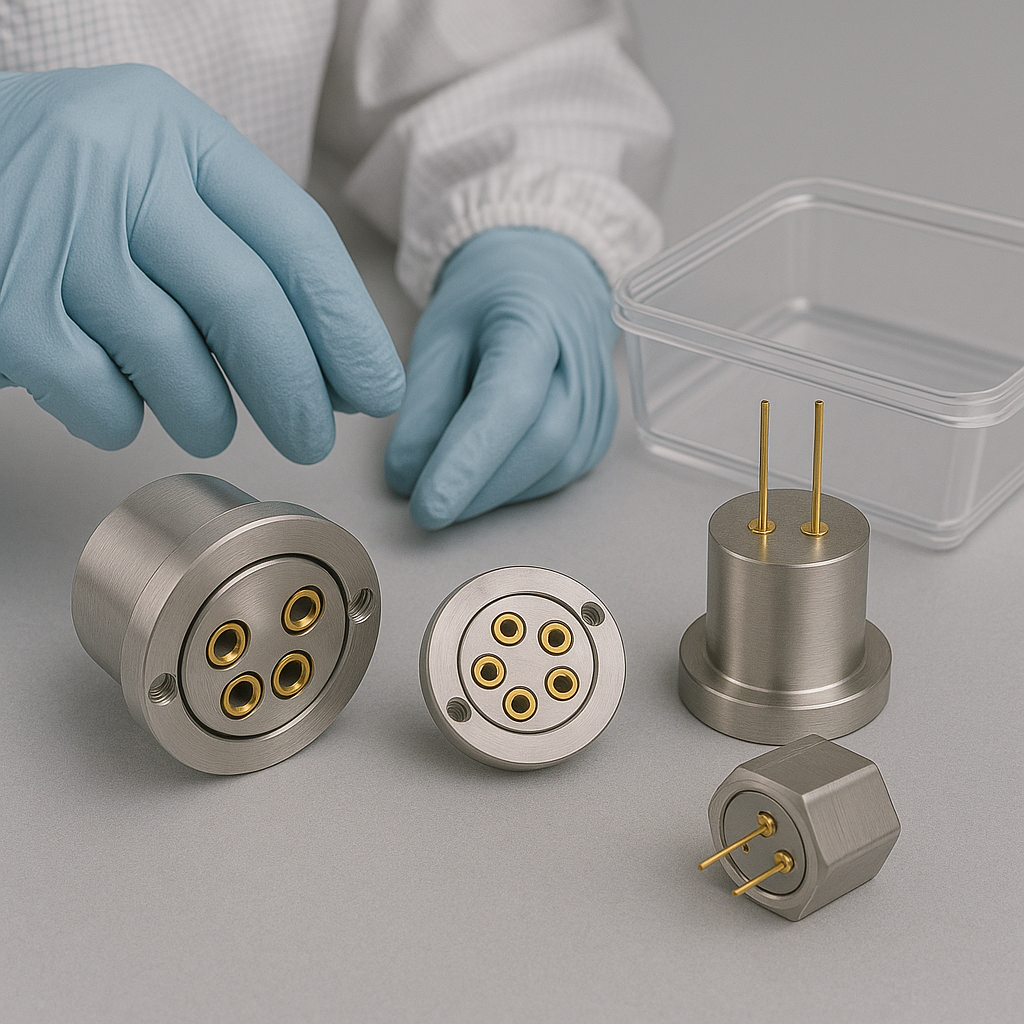
Inspection & Leak Testing
Our comprehensive inspection and leak testing services validate the structural and hermetic integrity of mission-critical assemblies. We apply rigorous testing protocols to ensure conformance with the most demanding industry specifications.
- Helium mass spectrometry leak testing with sensitivities down to 1x10⁻¹⁰ atm-cc/sec.
- Digital borescope inspection for internal feature verification and defect analysis.
- Non-destructive evaluation (NDE) services including industrial CT scanning and digital X-ray imaging available upon request.
- Pressure, vacuum, and burst testing for mechanical strength validation.
- Comprehensive inspection documentation and certification packages provided with each shipment.
We provide confidence and traceability through robust testing practices tailored to aerospace, defense, semiconductor, and medical applications.
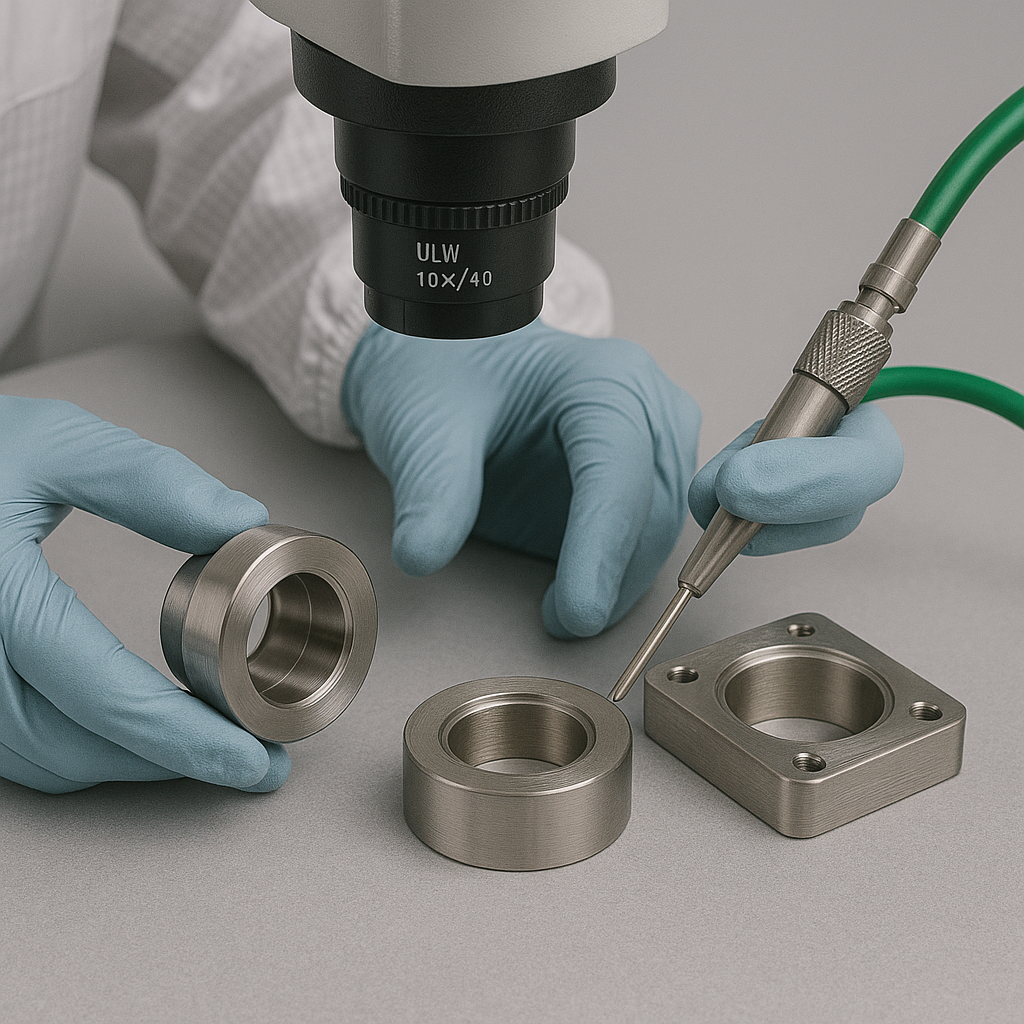
Engineering Design & Prototyping
Our engineering team provides end-to-end design support, from initial concept through prototyping and low-volume manufacturing. We collaborate closely with clients to optimize designs for manufacturability, performance, and reliability.
- 3D CAD modeling, mechanical tolerance analysis, and material selection consulting.
- Finite Element Analysis (FEA) for structural and thermal stress modeling.
- Rapid prototyping capabilities for concept validation, fixture design, and iterative development.
- Custom fixturing and tooling design to enable complex assembly and brazing operations.
- Design-for-manufacture (DFM) recommendations to optimize production scalability and cost-efficiency.
From design simulation to functional prototypes, we accelerate development timelines and improve product success rates with integrated engineering support.
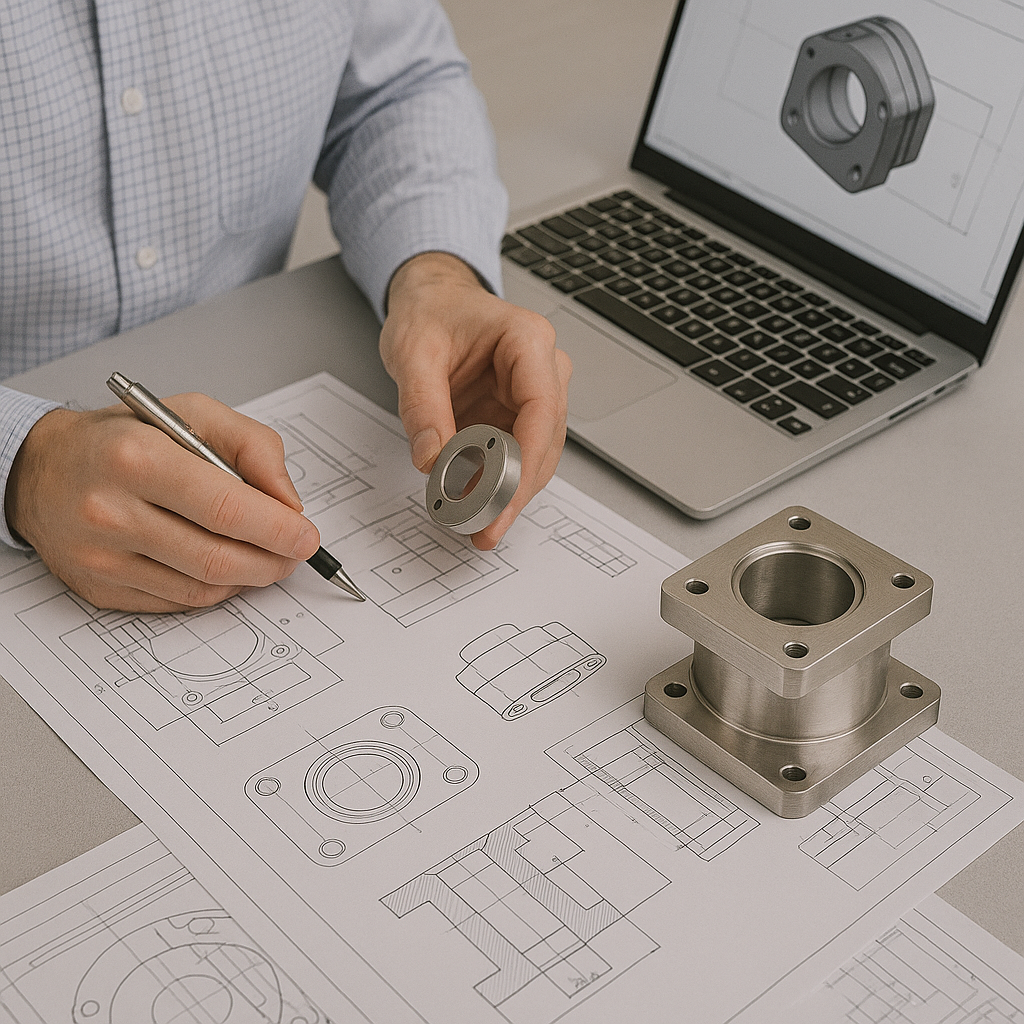
Have a Project in Mind?
Speak to our engineers for a custom quote or feasibility discussion.
Contact Us